Artificial Intelligence: these days, it’s hardly an exaggeration to say there’s never a day we don’t hear about AI in the news. Among the various forms of AI, “generative AI,” which can learn from data and create original digital content, is expanding and permeating our world at a dizzying pace that far exceeds our expectations. As you may know, discussions are already widespread about how this emerging form of AI could contribute to a variety of roles and fields—from relatively straightforward tasks such as writing text to highly creative endeavors such as art or video production and even consulting services that have traditionally depended on the deep expertise and experience of professional teams.
With so much buzz about generative AI across the globe, some may be surprised to hear, “In fact, the manufacturing sector is also highly compatible with generative AI.” The industry faces pressing goals, such as boosting productivity through digital transformation (DX) and achieving carbon neutrality, and you may wonder, “Really? Generative AI, too?” Yet Ryo Tanabe, from the Connected Products Development Dept., Customer Success Division, Customer Success & Service Business Group at Hitachi Industrial Equipment Systems, explains the reason as follows:
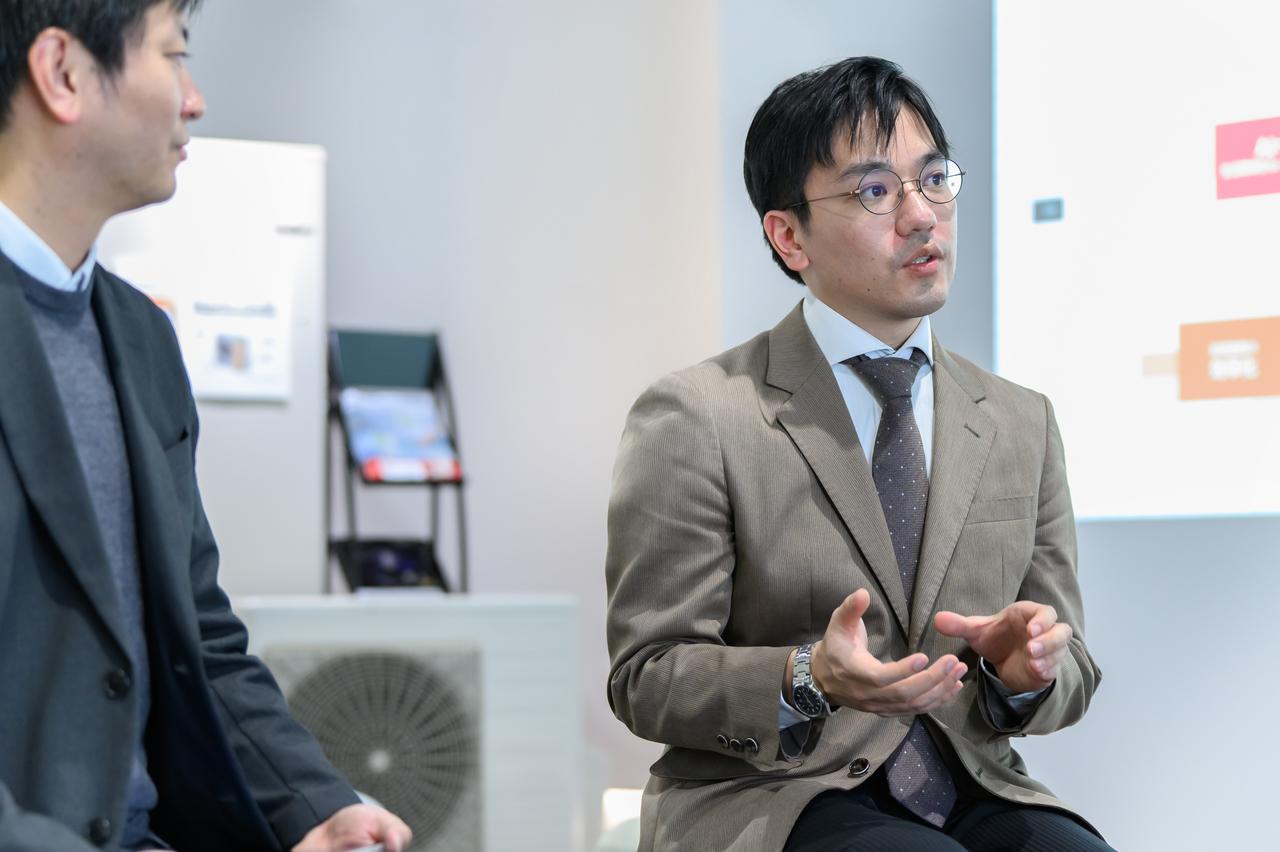
“The manufacturing floor is characterized by relatively clear needs and challenges. One part of that is
creating an environment in which operators—regardless of their level of experience—can carry out tasks smoothly. Detailed manuals exist for every aspect of factory operations, such as blueprints and operation schedules. Also, unexpected events tend to be rare, so we can use the data we’ve gathered to keep operations running efficiently. In that sense, I believe this is why AI and manufacturing sites are such a good match.”
New maintenance staff who are unfamiliar with the work environment often turn to experienced staff for advice when problems arise, which can place increasing burdens on their colleagues if it happens repeatedly. However, by implementing generative AI it becomes possible to communicate directly with the industrial equipment in place. The AI can answer all kinds of questions related to operations or equipment maintenance and offer guidance on resolving issues. In other words, your smartphone could effectively function as a “virtual senior colleague,” providing robust, around-the-clock support for any expected challenges.
Next-Generation Solutions Born from FitLive*
Introducing generative AI to the manufacturing floor—while it may be a perfect match in theory, it’s not something that can be achieved overnight. That’s where Hitachi Industrial Equipment Systems has a major advantage: the existence of “FitLive.” Since 2017, the company has been shipping connected products—including compressors and inkjet printers equipped with standard IoT (Internet of Things) capabilities. FitLive is the remote equipment monitoring service for these industrial devices, collecting and analyzing real-time operating data to track their status. This big data is used for early detection of potential malfunctions, proposing maintenance support measures, saving energy, and optimizing equipment operations.
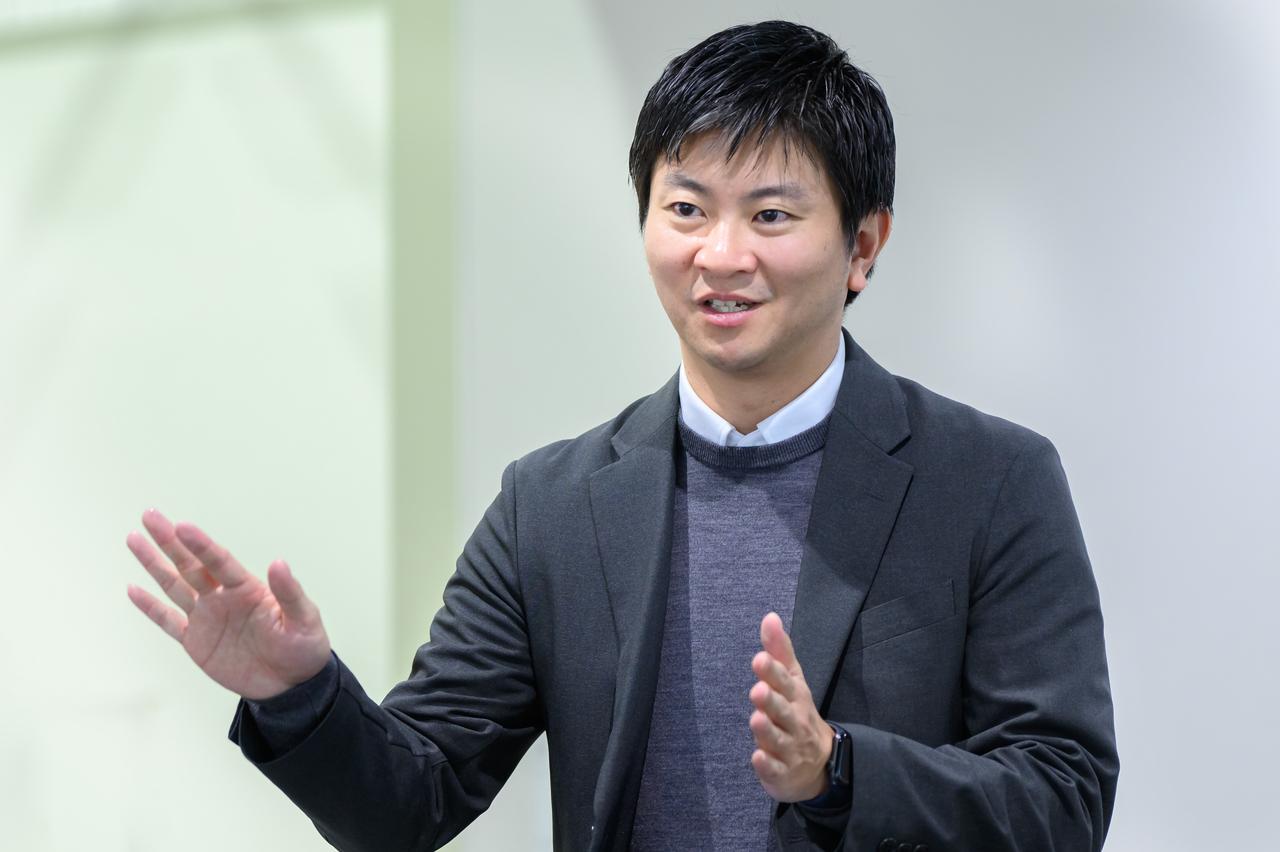
“Since we first introduced the service, FitLive has rapidly expanded, and we’re now connected to around 20,000 units, starting with compressors,” says Yusuke Nakagawa, from the Customer Success Strategy Dept.,Customer Success Division, Customer Success & Service Business Group at Hitachi Industrial Equipment Systems. “By integrating IoT-based data collection and analysis, we can understand the lifespan of each part that makes up the industrial equipment. This lets us recommend optimal maintenance intervals and, by extension, helps reduce downtime for our customers.”
“As the deployment of FitLive expands to more factory floors, the number of devices it monitors is also increasing. Naturally, there are limits to what the human eye can handle alone, which is why we place great importance on AI support. For example, if we need to monitor 1,000 or 2,000 units, AI’s biggest strength lies in its ability to instantly pinpoint, ‘This part of this product is malfunctioning.’ In that sense, I believe AI—especially generative AI—has a strong compatibility with manufacturing.”
“Until now, our service engineers would visit our customers’ sites to perform inspections and directly explain, ‘Here’s the current status of your equipment.’ But if generative AI can learn and become more adept in this area, I believe we’ll be able to provide our services more conveniently and on a broader scale.”
Manufacturing and AI: by combining the distinctive strengths of both and generating synergy, a completely new next-generation solution is now taking shape. The name of this project is “Talkative Products.”**
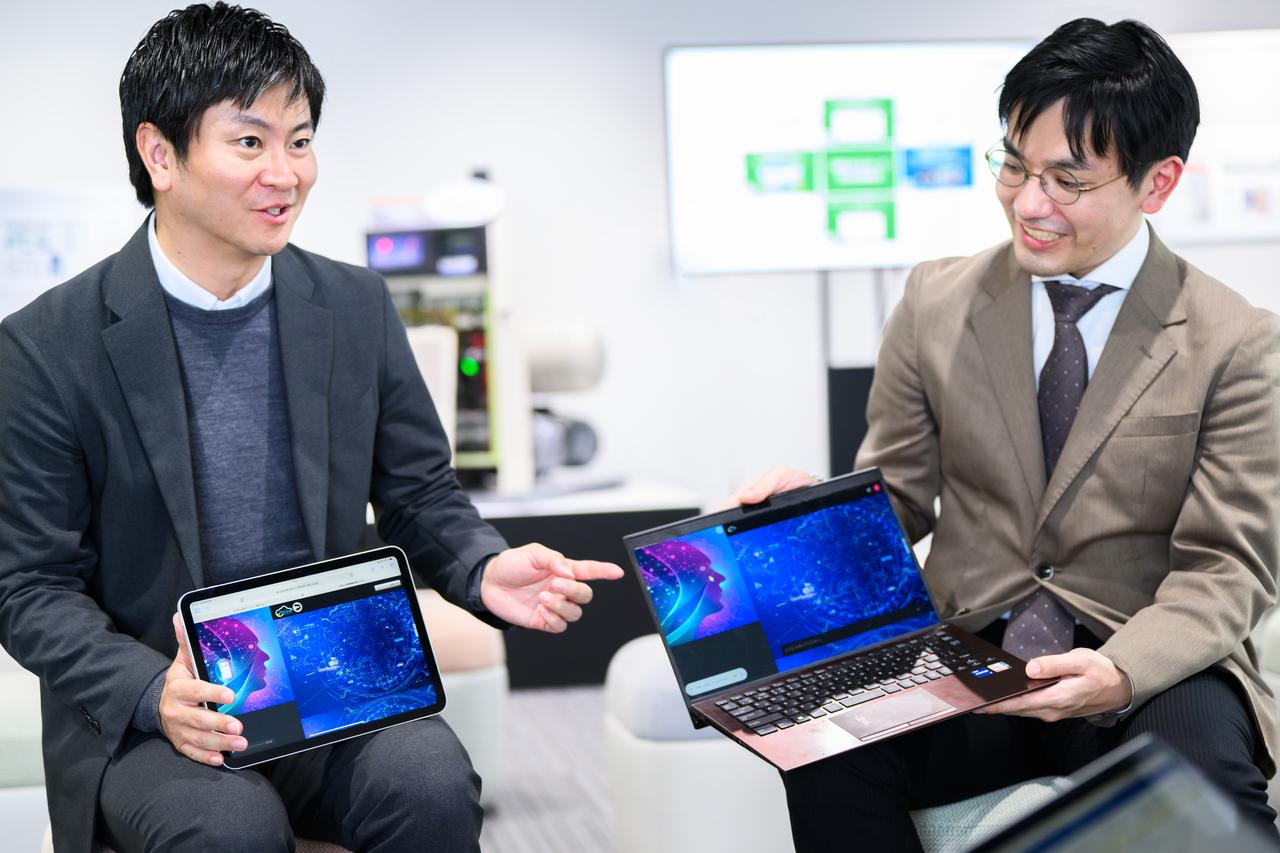
Talkative Products**: Unlocking the Future Through Being “Talkative”
Using the IoT-powered real-time equipment monitoring service “FitLive”* as a foundation, Hitachi Industrial Equipment Systems (HIES) is developing a next-generation solution called “Talkative Products.”** We use the term “talkative” because it typically describes someone who enjoys engaging in conversation and expressing their thoughts freely. It conveys a sense of openness and willingness to communicate. Instead of a human operator, generative AI will respond to inquiries related to the operation and maintenance of industrial equipment in a voice-driven, conversational format—maximizing each customer’s “successful experience.”
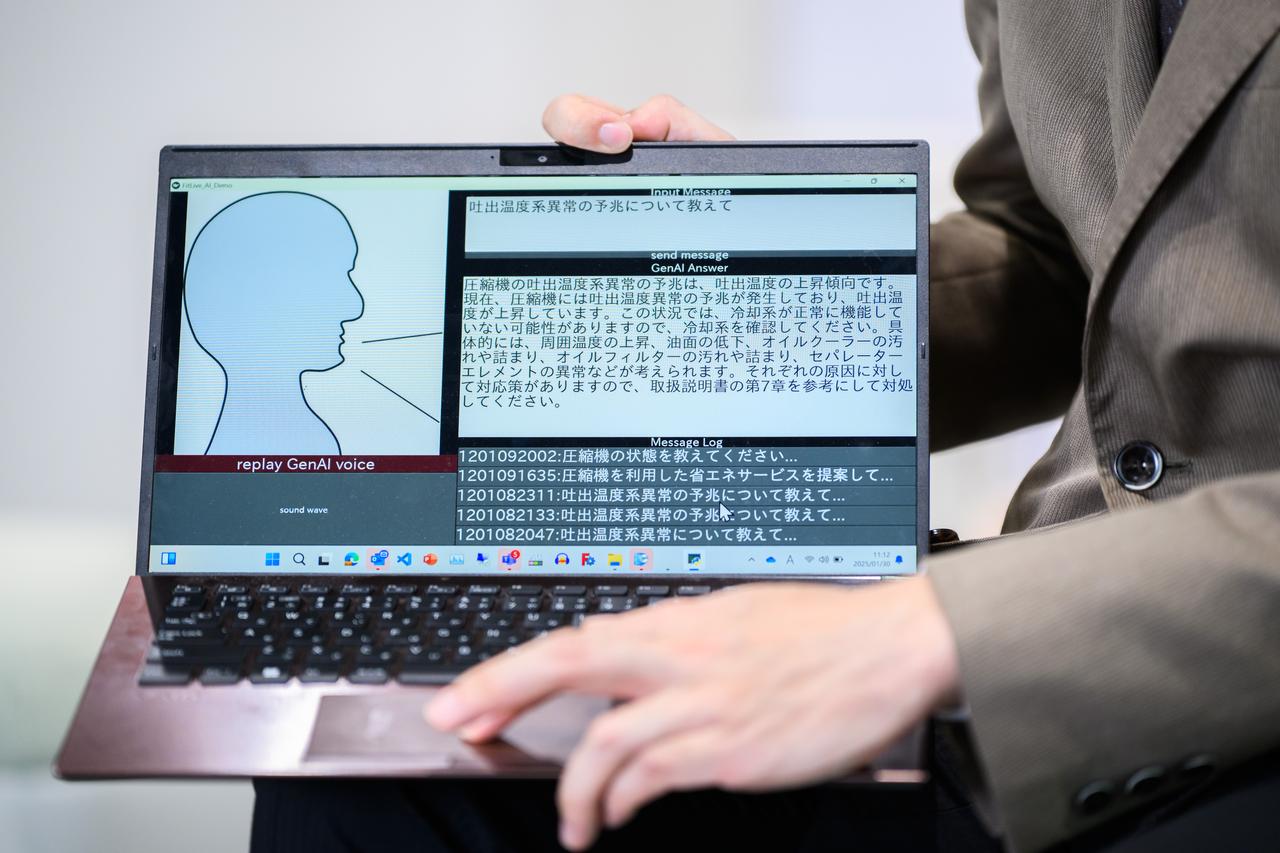
User interface from the early development of Talkative Products. This prototype was used to refine the necessary features and layout, and traces of it remain in today’s interface.
“Customers who have purchased and are using our products find machine maintenance and management especially burdensome and challenging. When an issue arises, they must check what kind of error has occurred and what sort of upkeep is necessary by reading the instruction manual—or call in a service engineer to inspect the situation on-site. That’s always been the norm.”
So says Nakagawa.
“But if you have Talkative Products, whenever something goes wrong, you can consult with the generative AI first. It already covers everything included in the instruction manual, so it’s capable of answering highly technical questions as well. We think that’s what makes this solution so appealing. Additionally, in cases where our dealers or sales partners cannot offer immediate support, Talkative Products would be highly effective.”
Strengthening AI with “Knowledge Structuring”
One key factor in using generative AI securely and safely is how its database, which contains vast amounts of data, is trained. No matter how convenient the technology may be, if the underlying database does not contain trustworthy information, it can lead to new issues rather than solving existing ones.
So what kind of “training” is Talkative Products using?
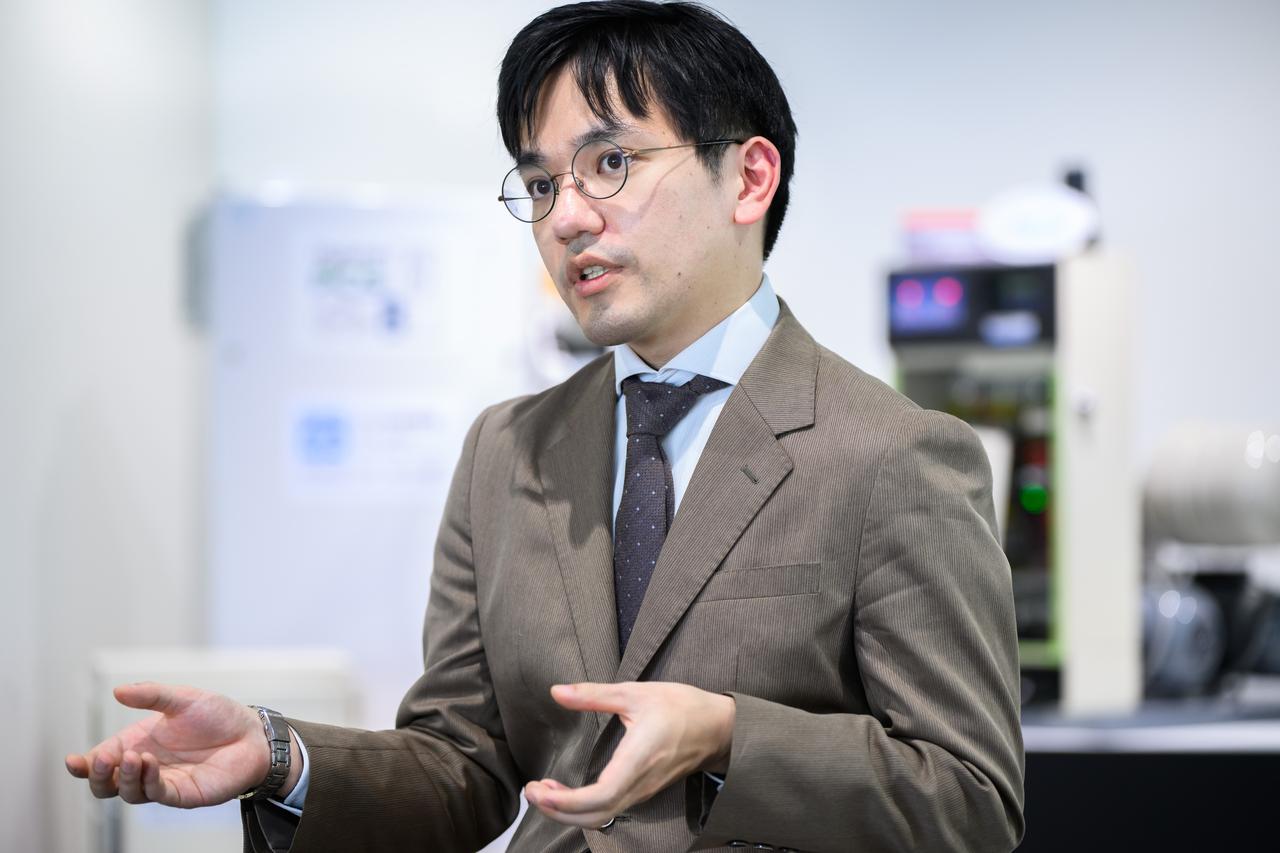
Tanabe explains:
“[As a prerequisite] we are not fine-tuning the AI itself, such as with large language models (LLMs), and we have a clear reason for that. We deal with multiple types of industrial equipment, each with different models and variations. If we lumped them all together, there’s a risk that the AI would respond to a question about an inkjet printer using data about a compressor, for example.
That’s what we call ‘hallucination.’ People often call it ‘lying,’ but I think of it more as ‘misunderstanding.’ When the AI acquires unnecessary knowledge, it may give irrelevant answers. We’re being extremely careful about that as we develop Talkative Products.”
In this context, the backbone of the database is made up of internal documents such as user manuals and service manuals for various types of industrial equipment. To make these documents easier for a generative AI to learn, they are being converted into more structured data—for example, by turning procedures into flowcharts. During the research and development phase, the team also rigorously evaluates the accuracy of the AI’s responses, and in some cases even adds extra information not found in the manuals to further improve precision.
“Some people call it ‘knowledge structuring,’ and I believe how we transform the company’s vast information into a database is the most crucial aspect of our technology,” Tanabe explains.
Delivering Personalized Services
So how does Talkative Products actually work?
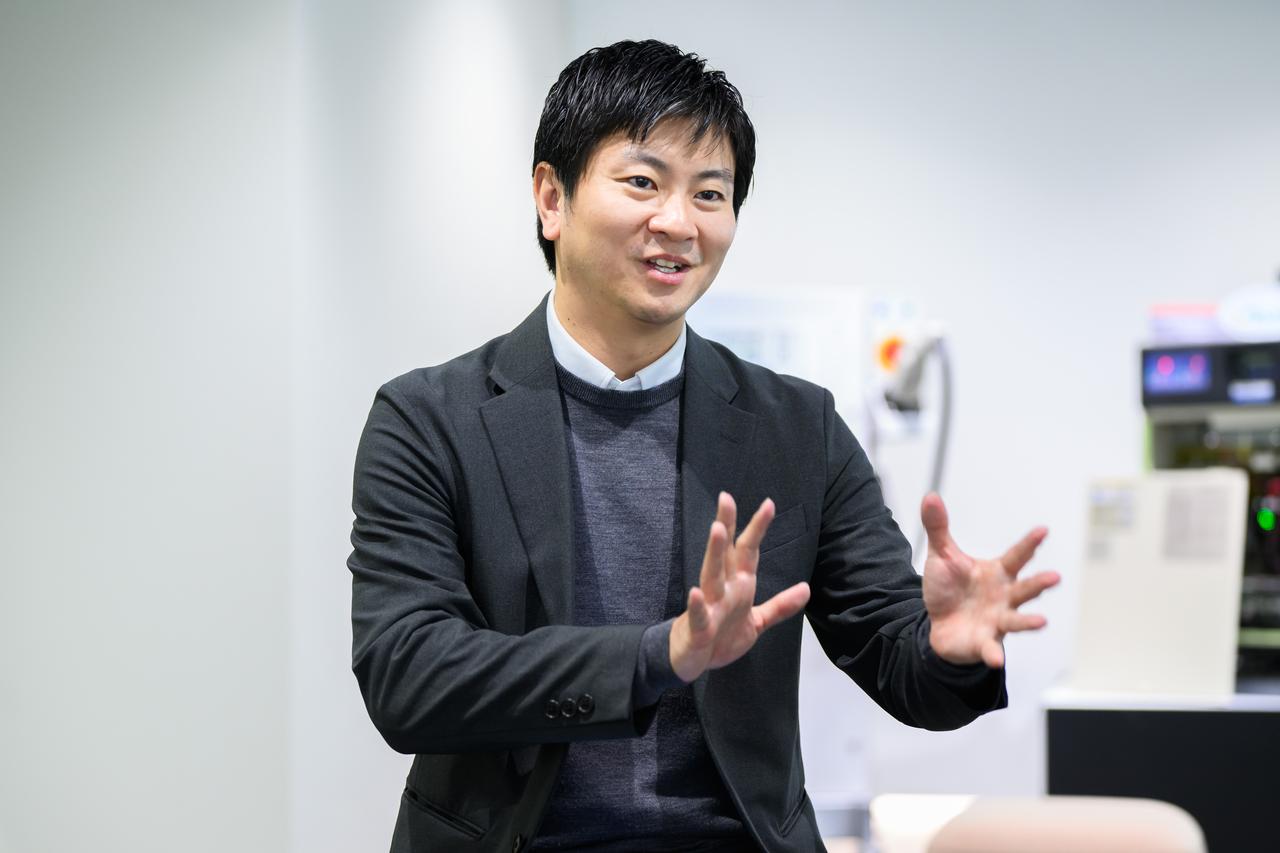
Nakagawa offers an example:
“For instance, with inkjet printers, the ink inside can dry out if it sits idle, requiring repairs or restoration that will interrupt a customer’s operations. But if you have Talkative Products installed and say, ‘How’s everything doing today?’ it might respond with something like, ‘Printer #X has been stopped for a week, so you may want to run it soon to prevent the ink from solidifying.’”
As of February 2025 (when this interview was conducted), Talkative Products is still under active development, but some parts of Hitachi Industrial Equipment Systems—such as the service division and certain factories—are already using it. Specific timelines for a broader release are yet to be determined. The plan, however, is to expand usage in stages throughout the company, its partner distributors, and dealers, and ultimately make it available to the most important users of all: the customers.
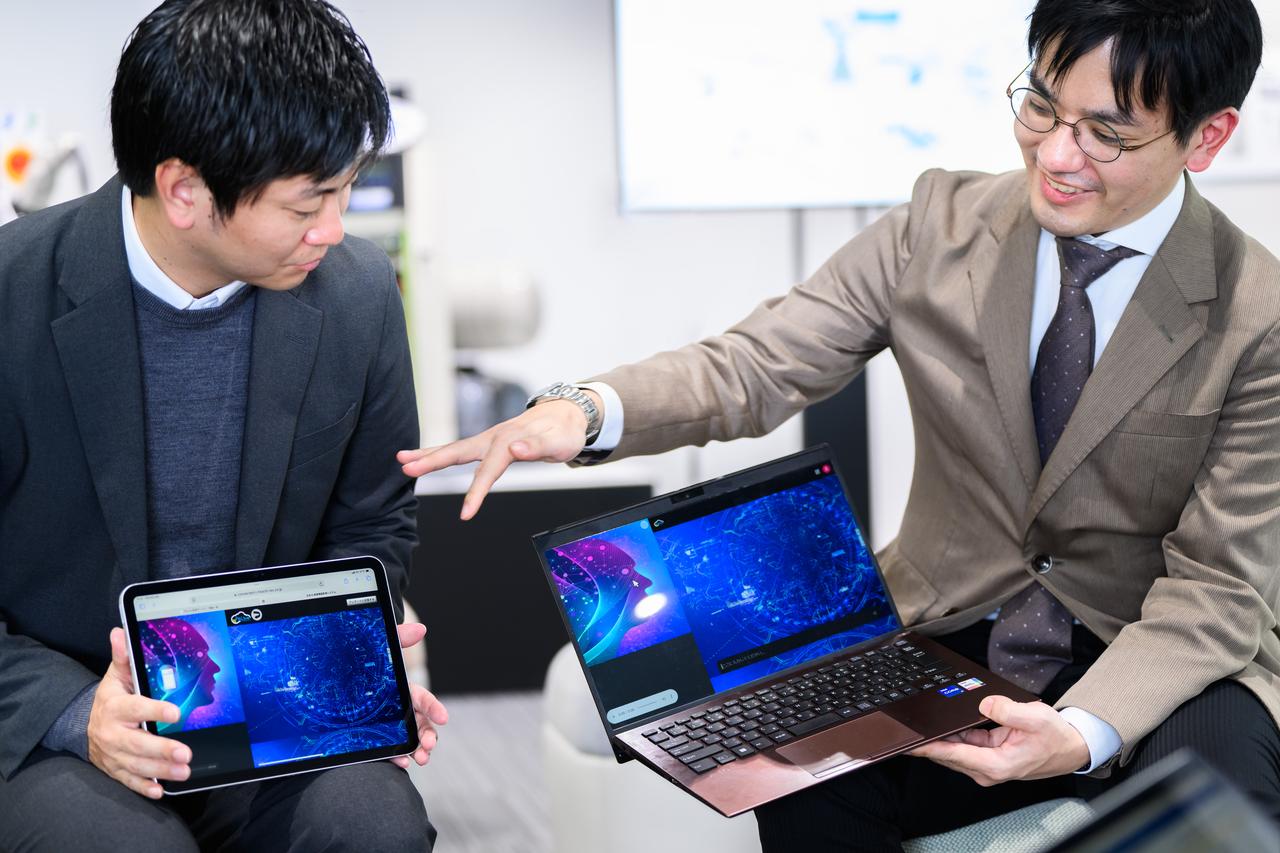
“We at Hitachi Industrial Equipment Systems handle everything from designing and manufacturing industrial equipment to sales and maintenance. Because we have access to all the data from these business areas—and because FitLive continually gathers detailed operating data—we possess an enormous amount of combined know-how, which is a major selling point,” says Tanabe.
Finally, Nakagawa sums up the interview with this vision:
“In the future, we’d like to take advantage of our overwhelming data and knowledge to offer truly personal services, optimized for each customer’s needs, through Talkative Products.”
The story of Talkative Products may have only just begun, but there’s plenty to look forward to in the near future.
* Note: “FitLive” is currently available only in Japan. Similar services are offered under different names in other regions.
**Note: “Talkative Products” is currently under development in Japan and has not yet been launched internationally.
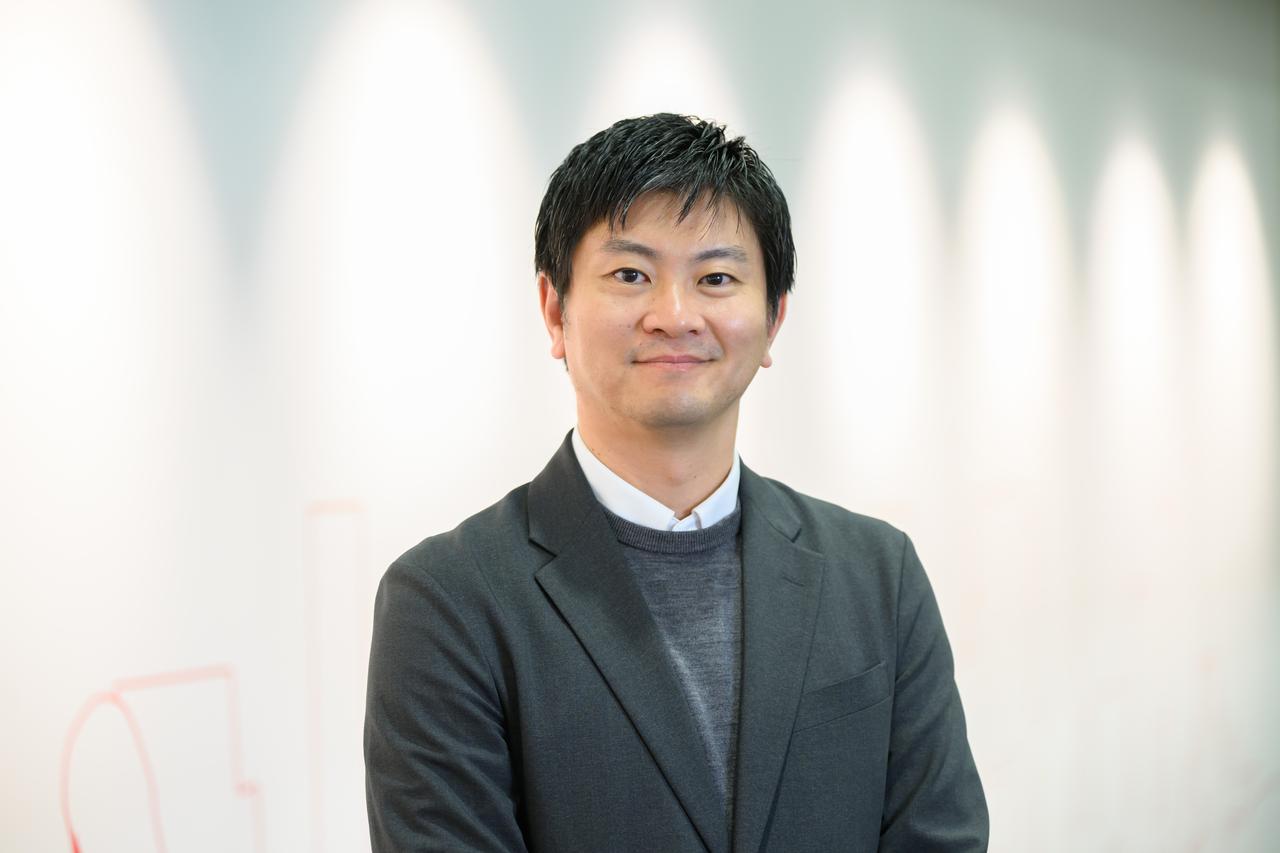
Yusuke Nakagawa
Manager, Customer Success Strategy Dept.
Customer Success Division,
Customer Success & Service Business Group
Hitachi Industrial Equipment Systems Co.,Ltd.
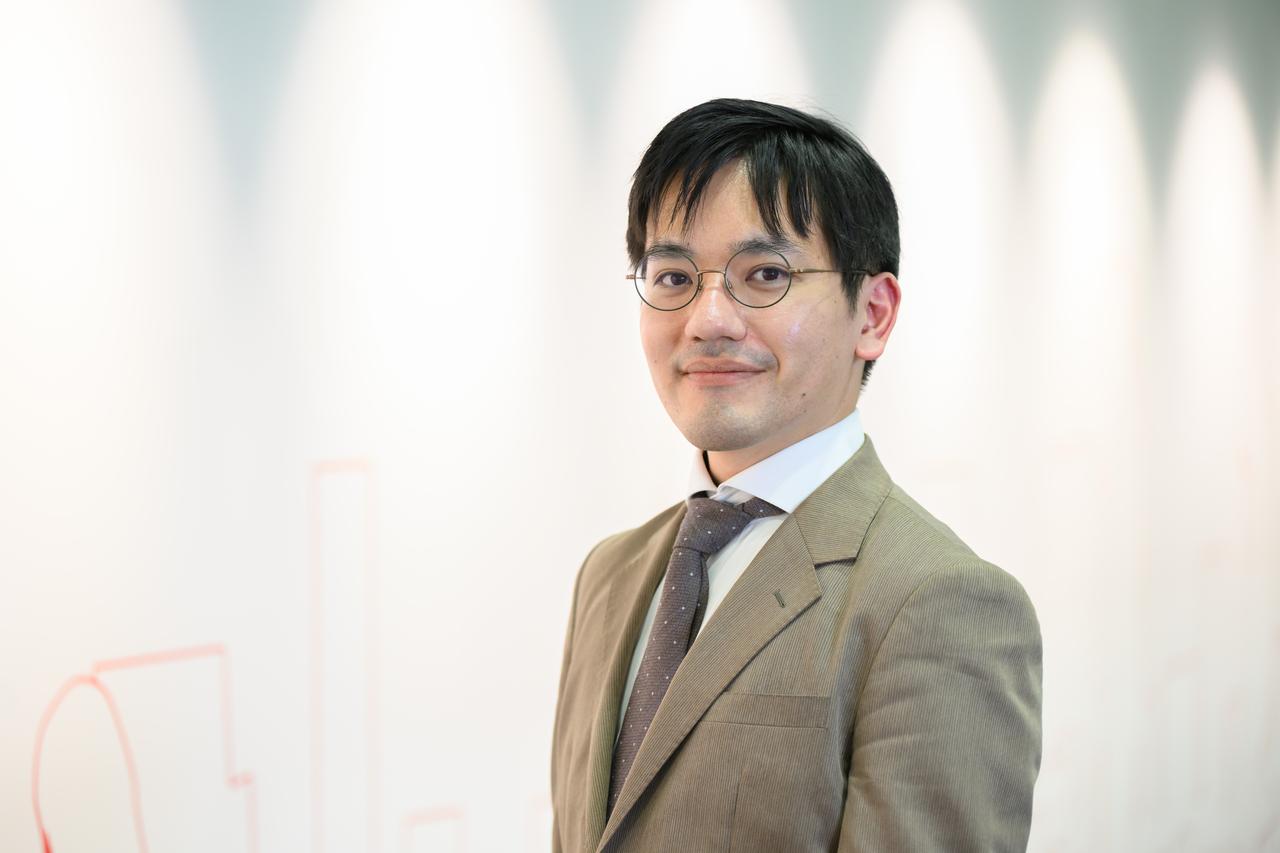
Ryo Tanabe
Engineer, Connected Products Development Dept.,
Customer Success Division,
Customer Success & Service Business Group
Hitachi Industrial Equipment Systems Co.,Ltd.