Manufacturing has a perception problem.
If I ask you to picture a factory, what comes to mind? Probably something like this: a dirty, dimly lit space. Rows of people turning wrenches. Workers walking in with lunchboxes. Temperatures so high that sweat pours down their faces.
That image belongs to decades ago. It’s not what manufacturing looks like today.
Many Americans have heard the phrase “not your father’s Cadillac.” It was meant to challenge assumptions and show how something traditional had evolved into something more modern. That’s exactly what we need to do with manufacturing.
This isn’t the world of grease-stained uniforms and eight-hour shifts of wrench-turning. Manufacturing today is highly technical and increasingly digital, especially as the Fourth Industrial Revolution unfolds.
Our industry runs on automation, sequencing, ERP systems, quality tracking and real-time traceability tools, and it’s only getting more advanced.
Yet despite this transformation, we’re still struggling to fill skilled roles. Not because the jobs don’t exist, but because public perception hasn’t caught up. If we want to attract the next generation, especially Gen Z, we need to create the kind of work environment they want.
What do workers value?
It starts with understanding what employees want beyond a paycheck. According to McKinsey, the top three reasons people take jobs in manufacturing (other than compensation) are:
- Meaningful work
- Workplace flexibility
- Reliable coworkers
Let’s discuss a couple of those and some other ways to help shift people's perceptions of the industry.
Flexibility, even on the shop floor
Not every manufacturing job can be done remotely, of course, but that doesn’t mean we can’t offer flexibility.
Before moving to Tokyo this year to lead Hitachi Industrial Equipment Systems, I served as President and CEO of Hitachi Global Air Power. Like many in the industry, we found attracting and retaining talent harder.
We knew we had to make changes. We needed a workplace that reflected the future of manufacturing, not the past.
We modernized the Hitachi Global Air Power factory in Michigan City, Indiana (USA). We repainted and cleaned the facility to make it look like the world-class operation it was. We introduced cooling jackets and invested in comfort and efficiency upgrades. We also ran kaizen activities to improve processes and drive continuous improvement.
6S kaizen activities at Hitachi Global Air Power factory
We restructured shifts to offer more flexibility. Employees now work four 10-hour days, which usually gives them a three-day weekend. During periods of high demand, overtime is scheduled on Fridays instead of Saturdays, allowing employees to keep their weekends.
In Japan, our office employees benefit from flexible hours and “Refresh Fridays,” which are meeting-free Friday afternoons designed for focused work and catching up. Over time, I’d love to see our factories evolve in similar ways as we did in the U.S. Flexibility supports both productivity and morale, and it shows we value and respect our employees and their time.
These are just a few examples. But the message is clear. Even when people can’t work from home, we can still find ways to offer flexibility and respect their time.
Engage talent early
If we want to shape the future workforce, we need to start earlier.
At Hitachi Global Air Power, we partnered with Michigan City High School (Indiana, USA) to launch the Compressed Air Academy, a program developed with local government, schools, and other compressor and vacuum manufacturers. The academy gives students hands-on training and a pathway into technical careers starting in high school.
Programs like this build awareness, provide hands-on training and help shift the perception of manufacturing as a respected, future-forward profession.
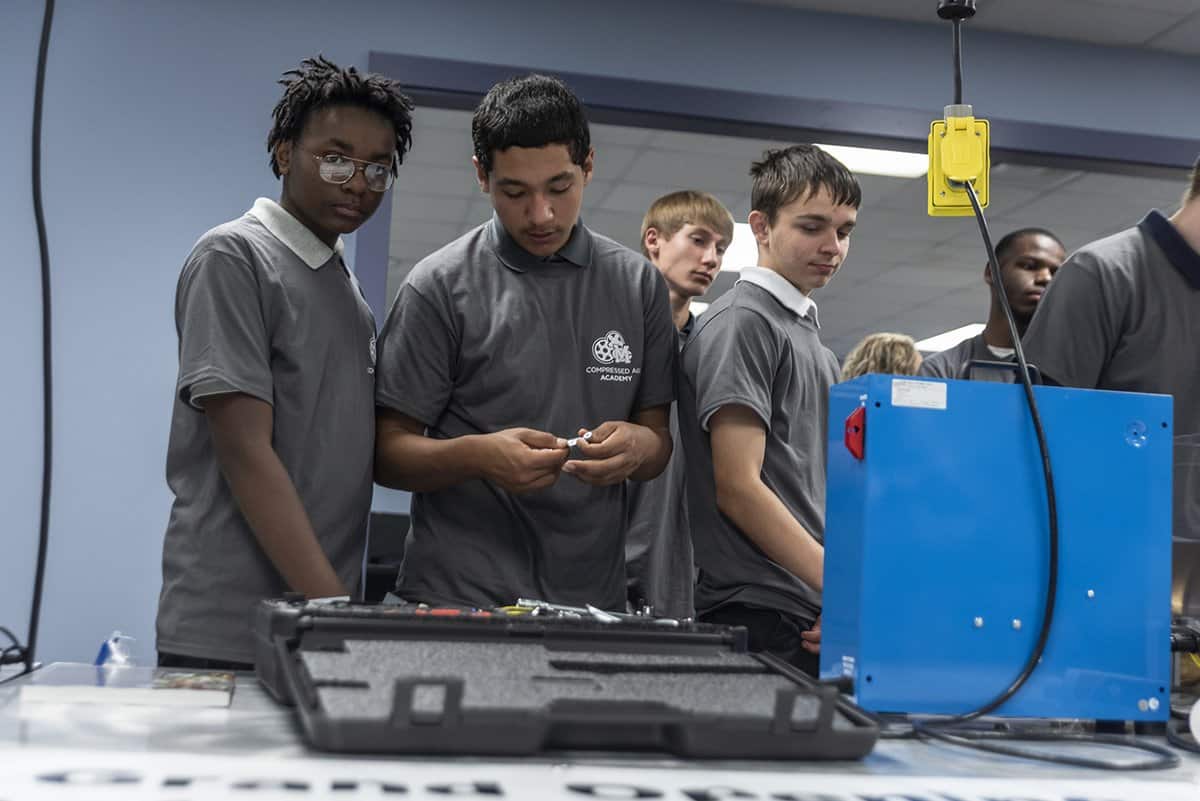
A scene from a Compressed Air Academy training session
Rewriting the “college or bust” narrative
Yes, we need engineers, STEM professionals and people with four-year degrees. However, not every role in manufacturing requires one.
We also need skilled tradespeople, technicians and operators. These roles don't always require a university degree, but they do require digital fluency, critical thinking and hands-on technical skills. And many of them pay well.
If we want to solve the skilled labor shortage, we need to treat these careers with the respect they deserve and tell young people that you don’t have to get a four-year degree to be successful in life. That story starts early, in schools and communities, and how we talk about our industry.
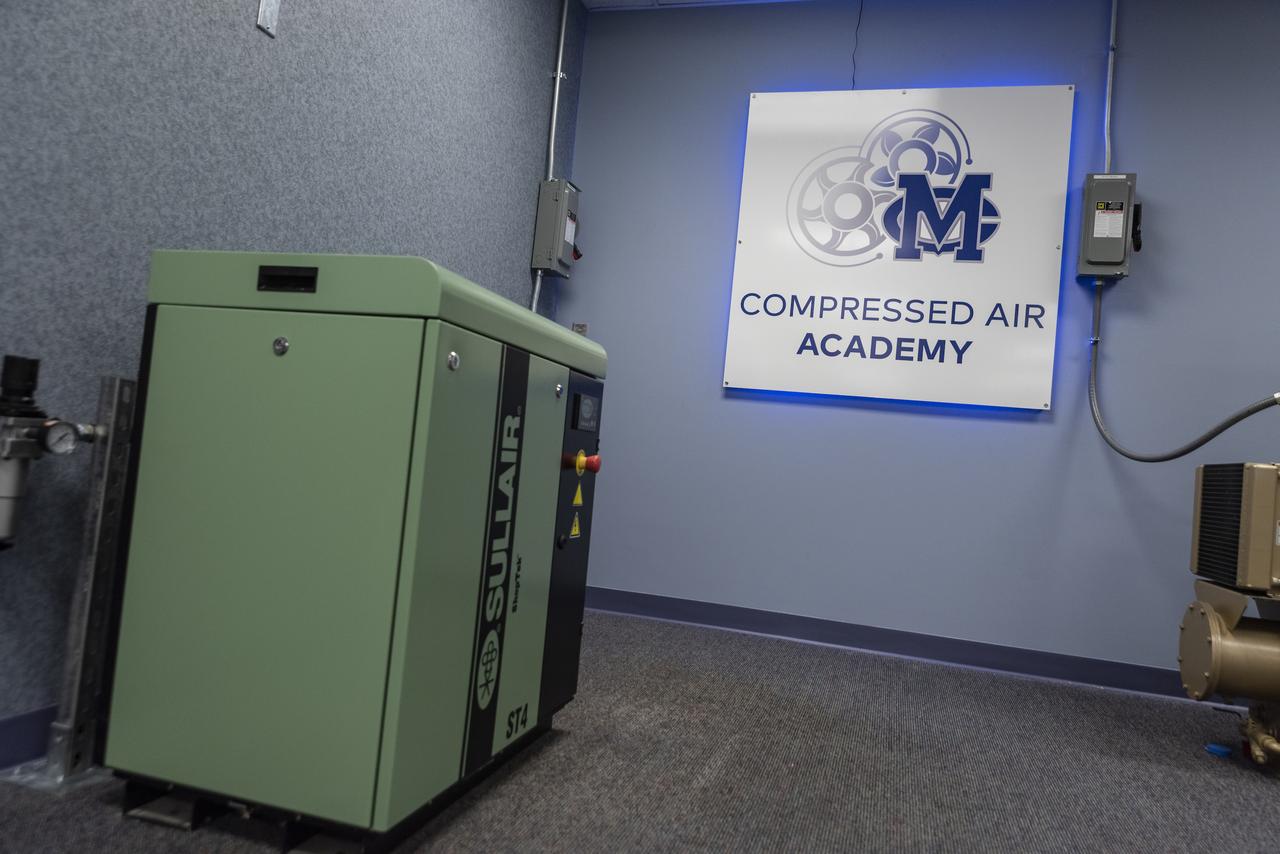
Providing meaningful work
Younger generations want to feel that their work contributes to something bigger than themselves. At Hitachi Industrial Equipment Systems, our corporate message and purpose reflect the broader impact we strive to make.
Every day, our teams — from the factory floor to engineering, product and program management, and more — create highly efficient, digitally connected products that support critical industries like food and beverage, automotive, pharmaceuticals, semiconductors and more.
We also provide opportunities to give back through our corporate social responsibility (CSR) efforts around the globe. Whether it’s a home build, river cleanup, tree planting, beach cleanup or other activity, employees can take part in making a positive impact in the communities where we live and work.
Employees participating in a riverbank cleanup as part of a CSR initiative
In our daily actions and long-term strategy, we are focused on putting purpose first.
Manufacturing isn’t stuck in the past. It’s building the future. Manufacturing has evolved so much, and it’s time the perception caught up.
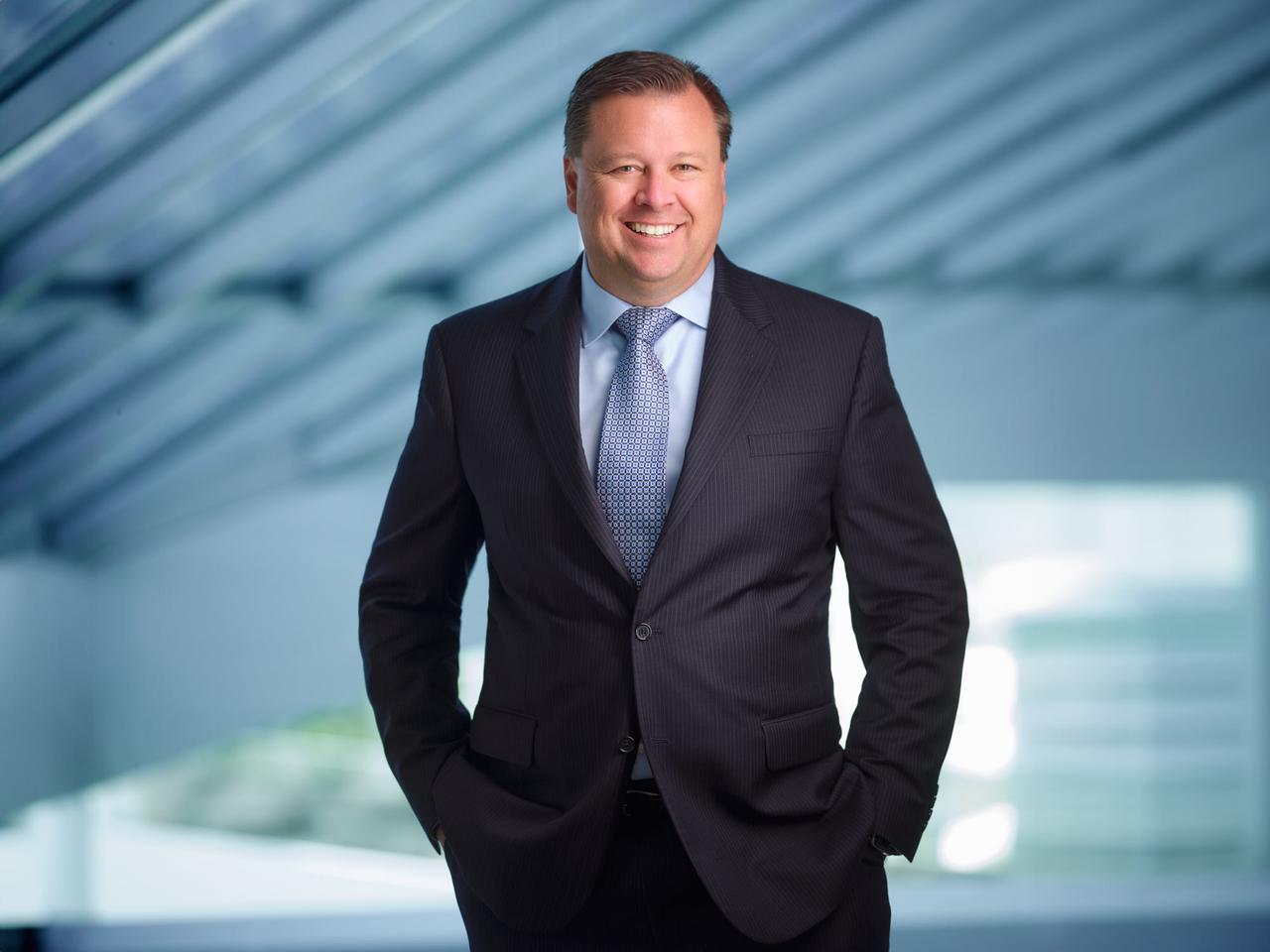
John Randall
President & CEO, Hitachi Industrial Equipment Systems
John formerly served as President & CEO of Hitachi Global Air Power (formerly Sullair) for four years. Prior to that, he was President of Sullair Asia for more than two years, and Vice President of Global Engineering for Sullair for more than six years.